The manufacturing sector is one of the main drivers in the economy, with most workers made up of permanent, contract, and casual workers.
Despite its importance, workforce management in manufacturing is a big concern due to the unstable nature of the sector.
Handling multiple shifts, attendance, labor law compliance, payroll processing, and turnover are all demand-streamlined processes. Most time-tested HR practices just can't handle it, resulting in inefficiencies, payroll mistakes, and compliance issues.
To solve these issues, manufacturing companies require strong HR management software. The appropriate solution will automate payroll, simplify attendance tracking, maximize shift scheduling, and maintain compliance with labor regulations.
This blog will discuss the most important workforce challenges facing the manufacturing sector and how HR software can resolve them efficiently.
How Do Workers Operate in the Manufacturing Industry?
Employees in manufacturing work in different conditions, such as assembly lines, machine operations, quality control, and maintenance. The employees are usually categorized under:
- Full-time Employees: They are permanent workers with fixed compensation and benefits.
- Contract Workers: Transitory employees recruited based on production needs and project requirements.
- Seasonal or Temporary Workers: Hired for limited times, especially for peak production periods.
- Skilled Technical Workers: Engineers, machine operators, and technicians crucial to production and maintenance.
Employees work in a highly organized setting where their working hours, pay, and compensation differs according to company regulations and labor laws. Attendance, payroll, overtime (OT), and compliance must be controlled methodically to maximize efficiency and employee satisfaction.
Challenges Faced by Workers Who Lack HR Software Knowledge
Though HR software offers many advantages, most manufacturing employees might be unable to utilize computerized systems because of a lack of technological knowledge, illiteracy, or unfamiliarity with HR software. These employees usually encounter the following issues:
Inability to Access Payroll Information
- Employees might not know how to view salary breakdowns, deductions, or overtime computations.
- They will mostly depend on supervisors or HR staff to inform them of their pay structure, which causes delays and confusion.
Trouble with Applying for Leave
- Employees not comfortable with online leave application procedures may be forced to use manual leave application procedures, which can get misplaced or disregarded.
- They may also not know their leave balance, making them frustrated upon being refused leave.
Missed Attendance Records
- Employees who do not know how to use biometric or electronic attendance systems may fail to clock incorrectly and lose part of their pay.
- They can have trouble updating attendance discrepancies because they cannot directly access HR systems.
Challenges in Shift and Work Schedule Updates
- Workers who do not use digital resources may not receive timely notifications for shift changes.
- Miscommunication about work schedules can lead to absenteeism or being given incorrect shifts.
Limited Communication with HR
- Staff may struggle to complain or request important documents like payslips and employment letters without knowing HR software.
- This can result in dissatisfaction as their problems may take longer to be addressed.
Do Workers Need HR Software?
A common misconception is that HR software is designed specifically for HR personnel. But it's wrong. Workers themselves experience significant advantages:
Payroll Transparency
- Employees can verify salary information, deductions, and overtime pay using kiosks, mobile devices, or self-service interfaces.
- Decreases wage conflicts through precise, computerized salary calculations.
Attendance & Leave Management
- Employees can use biometric readers, RFID cards, or mobile-based time clock systems to clock in and out.
- Automated monitoring ensures accuracy, decreasing fraud and manual mistakes.
Shift Planning & Communication
- Employees can see their shift schedules in advance and can ask for changes.
- Notifications alert workers of schedule changes, avoiding absenteeism.
Access to Benefits & Compliance Information
- Workers stay informed about minimum wages, overtime rates, leave policies, and labor laws.
- Helps prevent exploitation and ensures fair pay structures.
Self-Service for Workers
- Employees can request leave, access payslips, and raise HR concerns digitally.
- Reduces dependency on HR personnel for basic administrative tasks.
The Key Features of HR Management Software for Manufacturing
Consider HR software the ultimate toolbelt for manufacturing HR teams. The correct solution doesn't merely make paperwork easier—it maximizes workforce efficiency. Here's how:
Workforce Scheduling & Shift Management
- Manufacturing processes usually operate on several shifts, such as night shifts, overtime, and rotating shifts. Handling this manually can be disorganized and prone to errors.
- HR software offers automated scheduling capabilities that balance workloads, provide equitable shift allocation, and maximize productivity.
- Advanced scheduling features allow managers to adjust shifts according to production requirements dynamically, reducing idle time and labor costs.
- Staff can see their shift details and trade shifts (with approval) and get real-time alerts, reducing last-minute absences.
Time and Attendance Tracking
- Outdated punch-in/punch-out methods, such as buddy punching, are now unnecessary and easily exploited. Advanced HR software complements biometric readers, RFID-enabled check-in systems, and cell phone GPS for off-site workers.
- Robotic time monitoring ensures precise payroll computations, deters unauthorized overtime, and makes attendance records transparent.
- Integration with shift scheduling ensures smooth working time tracking, minimizing administrative time and payroll contention.
Payroll Automation
- Manufacturing payroll processing is sophisticated because of differential wage structures, overtime policies, bonuses, and compliance.
- HR software automates payroll calculations so employees can be paid promptly and properly.
- Direct integration with tax compliance helps businesses comply with the law. Thus, the risk of incurring penalties for default is eliminated.
- Employees can see electronic payslips, tax documents, and reimbursement history using self-service portals, reducing HR loads.
Compliance and Safety Management
- Production businesses must adhere to severe safety rules, such as OSHA and labor regulations. HR software will meet compliance needs by monitoring safety training, certifications, and accident reports.
- Automatic reminders are provided to HR groups for employee certification or compliance papers expiring soon.
- Incident report features enable organizations to document in-the-workplace incidents, conduct safety audits, and implement remedial measures, reducing the potential for legal claims.
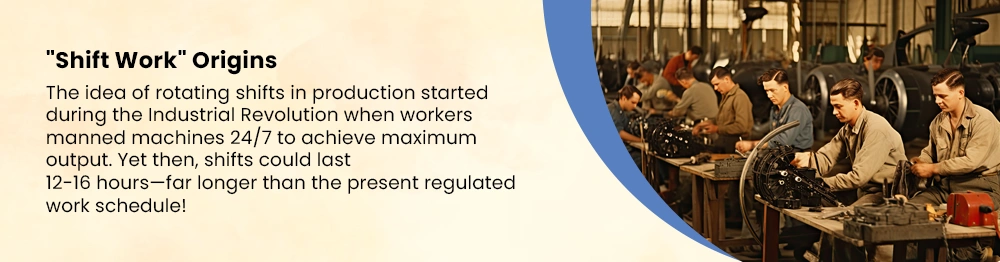
Bridging the Digital Gap for Workers
In order to make HR software accessible to all employees, manufacturing firms should adopt the following measures:
Training & Awareness Programs
- Carry out workshops and in-service training to acquaint employees with HR systems.
- Offer multilingual user interfaces to assist workers who are not conversant in the default system language.
Kiosk & Mobile Accessibility
- Implement easy-to-use kiosks in the factory grounds where workers can monitor their salary, attendance, and leave status without using personal devices.
- Develop mobile apps with simple navigation for workers who own smartphones.
HR Assistance Desks
- Designate HR personnel to assist workers with software-related queries and issues.
- Provide step-by-step instructions in local languages to enable workers to comprehend digital processes.
By solving these issues, manufacturing businesses can make sure that even technologically illiterate workers are able to take advantage of HR software, resulting in improved workforce management and employee satisfaction.
Challenges for HR in the Manufacturing Industry
HR professionals face several issues when managing a manufacturing workforce, including:
1. Complex Payroll Processing
- Manufacturing companies deal with several systems of wages, including piece-rate wages, hourly wages, and daily wages.
- Overtime (OT) calculations should include weekdays, weekends, and holidays differential rates.
- Insurance, tax, and benefit deductions add a layering complexity.
- Processing errors in payroll can create legal disputes, disaffection of employees, and loss of funds.
- Manual payroll processing can result in late payments, affecting employee morale and turnover.
2. Employee Turnover & Retention Challenges
- Frequent turnover due to contract-based jobs, fluctuating demand, and demanding work environments.
- Recruitment and rehiring struggles put extra pressure on HR teams, increasing costs and administrative workload.
- Workforce gaps caused by high turnover lead to reduced production efficiency and operational disruptions.
- Lack of employee engagement and poor communication create dissatisfaction and a sense of disconnect from management.
- Limited career growth and upskilling opportunities make it difficult to retain skilled workers in the long run.
- Rising hiring and training expenses due to high turnover negatively impact overall business profitability.
3. Ensuring Compliance
- Workplace legislation varies from area to area and comprises complex wage laws, working conditions, overtime, and employee compensation.
- Non-conformity will result in huge fines, legal sanctions, and company reputation harm.
- Manufacturing firms should see that contract and temporary workers are paid reasonably per government rules.
- Manually auditing payroll registers and attendance records poses a greater risk of compliance failure.
4. Workforce Data Management
- Handling thousands of employee records manually is error-prone and inefficient.
- HR offices must have updated information about the employment record, training, certifications, and performance.
- Incorrect accounting can lead to payroll errors and compliance problems.
- HR teams struggle to aggregate and analyze worker information to use for decision-making.

How Does HR Management Software Solve These Challenges?
The right HR software provides a comprehensive solution by:
1. Automated Payroll & Compliance Management
- Calculates wages accurately based on work hours, shift differentials, and overtime rates.
- Ensures compliance with minimum wage laws and tax regulations.
- Reduces payroll errors and disputes by providing transparent salary calculations.
2. Digital Attendance & Shift Tracking
- Uses biometric scanners, RFID, and mobile-based attendance tracking to prevent fraud.
- Provides real-time attendance data, helping HR plan workforce allocation.
- Automatically assign shifts based on production needs and workforce availability.
3. Leave & Absenteeism Management
- Allows workers to apply for leave digitally, reducing paperwork.
- Tracks absentee patterns to help HR take corrective measures.
- Generates reports to optimize workforce planning and productivity.
4. Employee Self-Service & Communication
- Enables workers to check payslips, leave balances, and work schedules from mobile apps or kiosks.
- Provides a communication platform for HR to share updates and policy changes.
- Allows employees to submit grievances digitally, ensuring faster resolution.

The Price Tag: Is HR Software Affordable for Manufacturers?
HR software is not only a cost—it's an investment that will pay itself back. Pricing models differ, such as:
- Subscription-Based: Pay per user monthly or annually, suitable for scalable businesses.
- One-Time Payment: Greater initial expense but no ongoing charges, ideal for businesses that like to save costs in the long run.
- Tiered Pricing: Prices are based on the number of employees or features required, providing flexibility.
The Future of HR in Manufacturing: What’s Next?
The future of HR manufacturing is changing, and the pace is being set by technology. Here's what's next to come:
- AI & Machine Learning: Foretell workforce demand, streamline shift scheduling, and assess employee performance to enhance effectiveness.
- Cloud-Based HR Systems: Offer real-time access, improved data security, and convenient collaboration from remote locations.
- Data-Driven HR: More intelligent analytics will help firms make informed data-driven decisions regarding recruitment, retention, and employee happiness.
- Automation & IoT Integration: Next-generation HR software will be infused with IoT sensors on the shop floor, enabling real-time productivity and workplace safety measurements.
Ready to Transform Your Manufacturing HR Management?
Don't be held back by outdated HR practices. Modern HR software allows you to automate workflows, enhance compliance, and maximize employee engagement.
Welcome HR HUB – Manufacturing's One-Stop HR Solution
HR HUB is a full-scale Human Resource Management System (HRMS) designed specifically to serve the unique requirements of the manufacturing sector.
From shift management to auto-payroll, HR HUB integrates all the HR operations under one roof so that manufacturers can focus on productivity while maintaining seamless workforce management.